O modelo de Robot as a Service (RaaS ou robô como serviço) já é uma realidade, segundo o estudo da Coherent Market Insights, que estima que esse mercado vai atingir US$ 41,3 bilhões em 2028, pulando de US$ 12,6 bilhões em 2020. Mais do que o valor em si, o RaaS é inovador, sendo baseado em assinatura e permitindo que clientes industriais possam alugar os robôs em vez de comprá-los. Os pacotes incluem os equipamentos e softwares, além de vários modelos de precificação.
O site Robotics Casual destaca que o modelo é mais flexível, pois as soluções RaaS podem ser facilmente ampliadas ou reduzidas se a demanda mudar. A publicação lista as vantagens do RaaS e destaca que ele deve prosperar, acompanhando a adoção cada vez maior do conceito de Indústria 4.0, com redes privativas de telecomunicações e maior conectividade.
Robot as a Service ganha no preço e culturalmente
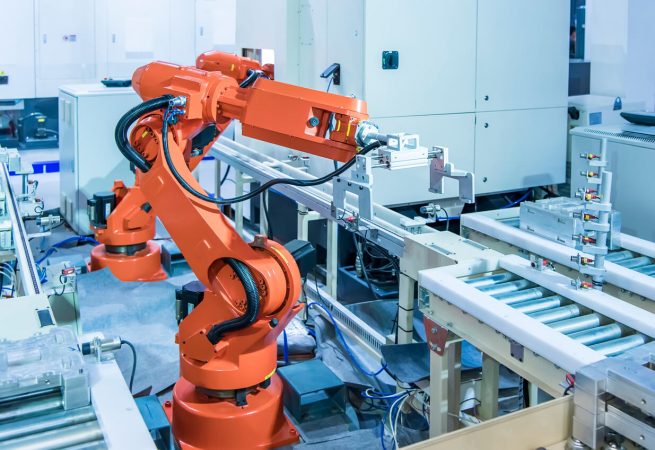
O primeiro ganho começa com a precificação, pois o uso do robô geralmente será cobrado de forma diferenciada, seja pelas horas trabalhadas ou seja pelos ciclos de execução de serviços. Independente disso, o mais importante é que o risco e a incerteza são assumidos pelo integrador do robô. Para o cliente industrial, isso significa que os custos são mais previsíveis e o valor econômico da integração do robô pode ser calculado antecipadamente.
Outro diferencial é cultural: a oferta de RaaS elimina a necessidade de convencimento de novos clientes para adotar a robótica em campo. Isso acontece porque não há investimento de capital (capex) e de todo um aparato auxiliar para incluir os robôs nas plantas. Os custos de operação (opex), assim como a manutenção, são assumidos pelas empresas especializadas na oferta do robô como serviço.
Redes privativas beneficiam Robot as a Service
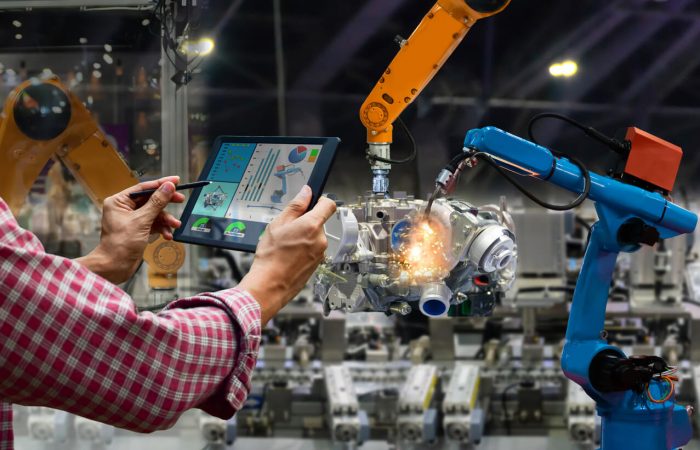
Como os robôs necessitam ser integrados a algum sistema de gerenciamento, as plantas que já operam com os conceitos de Indústria 4.0 levam alguma vantagem, pois isso significa que elas possuem um ambiente de conectividade ágil, em alguns casos com redes privativas de telecomunicações.
É o caso da Gerdau, que possui o primeiro projeto de uso de rede 5G no setor siderúrgico na América Latina. Desenvolvido em parceria com a Embratel, o empreendimento combina automatização, produtividade, flexibilidade, visibilidade, rastreabilidade, uso de dados e segurança nos processos, incluindo planejamento, produção e logística.
A inovação está sendo aplicada na planta industrial de Ouro Branco (MG), maior usina da empresa no mundo. As soluções serão viabilizadas por uma rede privada dedicada 5G e LTE 4G – quarta geração de tecnologia móvel de transmissão de dados – implementada pela Embratel.
Este é o primeiro projeto de uso do 5G no setor do aço na América Latina e a parceria entre Gerdau e Embratel tem como objetivo criar uma infraestrutura digital habilitadora para o desenvolvimento da indústria de aço do futuro.
No projeto, a Embratel está atuando lado a lado com a Gerdau para que a produtora atinja o próximo nível em sua digitalização, possibilitando a ampliação do gerenciamento e sensoriamento de ativos críticos, uso de carboxímetros conectados, caminhões autônomos e retroescavadeiras telecontroladas, além da monitoração inteligente por câmeras e drones para segurança preditiva.
Outra planta com essa pegada é a da Nestlé, em Caçapava (SP), com uma rede 5G habilitada pela Embratel, em parceria com a Claro e usando tecnologia de redes privativas Ericsson (Private 5G). O consórcio conseguiu ativar uma rede com conectividade segura de 4G e 5G de alta velocidade, que impulsionará a transformação digital principalmente de seu ambiente industrial da multinacional de alimentos.
Com a nova rede, a Nestlé poderá evoluir de uma fábrica automatizada para uma autônoma. Por meio do projeto, que utiliza frequências de uso experimental licenciadas pela Claro, todos os componentes da infraestrutura, desde as antenas até a rede core autônoma e o servidor, estão localizados nas instalações da Nestlé, o que significa uma rede 100% on premises.
Entre os benefícios da arquitetura está a operação de veículos autoguiados (AGV) na fábrica. Com redução na latência, o controle do equipamento passa a ocorrer quase em tempo real e de forma remota, possibilitando que seja usado com mais segurança, prevenindo riscos de colisões, informa a reportagem da Exame a respeito da fábrica.